In industries that rely on bulk material handling, unexpected flow issues can lead to production slowdowns, equipment damage, and costly downtime. Understanding how materials behave within your system is crucial to maintaining efficiency and avoiding disruptions. This is where Bulk Material Flow Testing comes into play.
The Problem: Bulk Material Handling Blockages
Blockages in bulk material handling systems are a common but preventable problem. Factors such as moisture content, particle size, and material composition can affect how substances move through chutes, hoppers, and conveyors. If these variables are not properly analyzed, materials may clump together, adhere to surfaces, or form obstructions, leading to system inefficiencies and financial losses.
Why Bulk Material Flow Testing is Essential
By conducting Material Flow Analysis, companies can gain a deep understanding of how their materials behave under different conditions. This testing involves:
- Measuring Flow Properties – Examining parameters like bulk density, cohesiveness, and angle of repose to predict material behavior.
- Simulating Real-World Conditions – Testing materials under controlled environments to replicate operational scenarios.
- Optimizing Equipment Design – Ensuring that chutes, silos, and feeders are designed to prevent hang-ups and promote smooth flow.
For instance, WTW Americas utilizes ASTM International-standard shear testers to assess bulk material flow properties, ensuring that equipment is tailored to specific material behaviors.
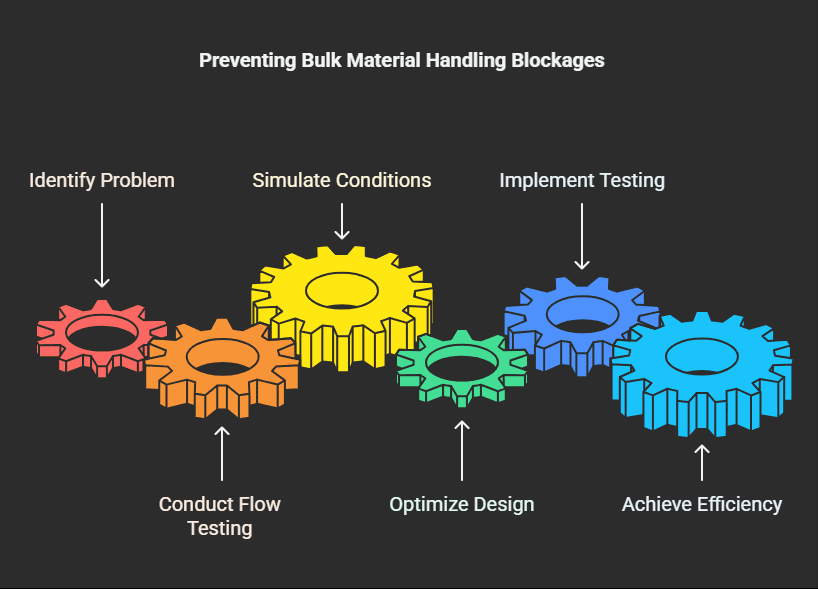
The Cost of Ignoring Material Flow Analysis
Failing to conduct thorough Bulk Material Flow Testing can result in significant financial repercussions. Some common consequences include:
- Frequent Downtime – Unplanned shutdowns due to blockages can bring production to a halt.
- Increased Maintenance Costs – Clearing blockages often requires manual intervention and repairs.
- Product Loss – Materials that become stuck or degrade due to poor flow can lead to waste and quality issues.
Understanding common flow problems, such as “rat-holing” and arching, is essential in designing systems that promote mass flow and prevent such issues.
How to Implement Effective Testing
To prevent costly disruptions, industries handling bulk materials should incorporate routine testing into their operational processes. Here are a few steps to consider:
- Conduct Preliminary Material Testing – Analyze new materials before integrating them into the system.
- Regularly Monitor System Performance – Identify early signs of flow issues and make adjustments as needed.
- Invest in Expert Analysis – Partnering with material flow specialists can provide insights that enhance system reliability and efficiency.
WTW Americas offers comprehensive services in bulk material and shear testing, utilizing advanced techniques to evaluate material flow characteristics and optimize equipment design.
Conclusion
Bulk Material Flow Testing is a proactive approach to preventing Bulk Material Handling Blockages. By understanding and addressing material flow characteristics, businesses can avoid costly disruptions, improve efficiency, and maximize productivity. Don’t wait for a blockage to disrupt your operations—implement Material Flow Analysis today to keep your systems running smoothly.
For more information on optimizing your bulk material handling systems, consider exploring WTW Americas’ approach to material flow optimization.